Topic:Multiscale Representation of the Microstructure Evolution and the Mechanical Properties of Ferritic Steel Grade during the Production Process
Speaker:Dr.Dirk Helm
Fraunhofer Institute for Mechanics of Materials IWM, Germany
Time:10:00-11:30 AM., Thurs., Aug. 16, 2012
Venue:Room 403, R&D Center, IMR CAS
Welcome to attend!
Multiscale Representation of the Microstructure Evolution and the Mechanical Properties of Ferritic Steel Grade during the Production Process
Dirk Helm1, Maria Baiker1,2, Pierre Bienger1,2
1 Fraunhofer Institute for Mechanics of Materials IWM, Woehler Str. 11, 79108 Freiburg, Germany, dirk.helm@iwm.fraunhofer.de
2 The Institute for Applied Materials - Reliability of Components and Systems IAM-ZBS, Karlsruhe Institute of Technology KIT, Engelbert-Arnold-Str. 4, 76131 Karlsruhe, Germany
ABSTRACT
After casting, the process chain for the production of semi-finished sheet metals consists of different process steps like hot-rolling, cold-rolling, heat treatment, and skin pass rolling. Thereafter, the semi-finished part is manufactured to a component by sheet metal forming operations like deep drawing. During such process chains, a strong evolution of the microstructure and the resulting mechanical properties can be observed. Due to the occurring finite plastic deformations and the accompanied increase in dislocation density during the cold rolling process, the grain structure is extremely deformed and the orientations of the grains are changed. In contrast to hot-rolled metals, the cold-rolled material shows recrystallization by temperature rise. The recrystallization processes are required to adjust the mechanical behaviour of the annealed material. For process optimization, it is essential to understand the combined process of cold-rolling and annealing: i.e. how the microstructure like the grain orientations evolves and also how that influences the mechanical behaviour. Only detailed knowledge about the microstructural evolution enables to find the optimal design of such process chains. During component production by deep drawing, the resulting material properties of the semi-finished product influence strongly the material behaviour in the manufacturing process.
In all, the production chain of components made of steel materials is very complex. For this reason, the precise modelling of such process chains is a challenge and requires an appropriate choice of the applied simulation model for each process step. For certain parts of the process chain like cold rolling, crystal plasticity modelling concepts seem to be appropriate for the accurate representation of the material behaviour including the texture evolution. The multiscale approach to represent the cold rolling process is based on a full-field unit cell model that considers the morphology and grain interaction of the polycrystalline microstructure. Unfortunately, this approach requires large computation times, which lead to the situation that not all parts of the process chain can be effectively represented by computational crystal plasticity. Thus, a useful combination between crystal plasticity based approaches and macroscopic modelling strategies seems to be a very promising way for the adequate representation of complex process chains.
In detail, a process chain of the mild deep drawing steel grade is studied in the present work. Here, the process chain consists of cold rolling, heat treatment, and deep drawing. First, selected experimental results like texture evolution and mechanical properties are discussed. Thereafter, different modelling concepts will be introduced to represent the observed phenomena in the manufacturing process. The last process step, the deep drawing operation, requires the solution of complex initial-boundary-value problems: For the industrial application where complex forming operations are simulated, the prediction of exact shapes, material flow, thinning, wrinkling, earing, and springback effects is a challenge, particularly when materials with complex textures and microstructures are involved. Therefore, a macroscopic finite plasticity model will be introduced. For bridging the gap between the micromechanical modelling concept for the process chain of semi-finished products and the macroscopic simulation of deep drawing, the so-called virtual laboratory [1-3] is applied: On the one hand, the virtual testing on the basis of crystal plasticity based calculations assists the macroscopic material modelling. For example, in order to introduce an appropriate yield function or hardening model. On the other hand, the material parameters of the macroscopic model are identified. Finally, simple deep drawing operations like forming of a circular cup are simulated with the macroscopic model and the simulation results are compared to the experiments.
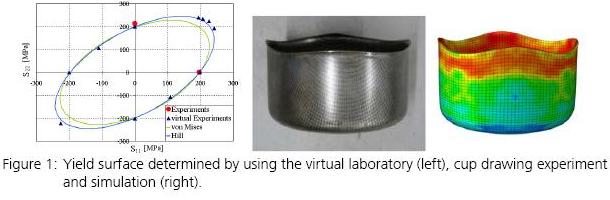
References
[1] Butz, A., Lossau, S., Springub, B., Roters, F., On the Modeling of Dual Phase Steels: Microstructure-based Simulation from the Hot Rolled Sheet to the Deep Drawn Component, International Journal of Material Forming 3, 2010, p. 73-76.
[2] D. Helm, A. Butz, D. Raabe, P. Gumbsch, Microstructure-based Description of the Deformation of Metals: Theory and Application. JOM Journal of the Minerals, Metals and Materials Society, 2011, Vol. 63, p. 26-33.
[3] M. Baiker, D. Helm, Crystal plasticity assisted calibration of finite plasticity model and the application to sheet metal forming. steel research international, Special Edition: 10th International Conference on Technology of Plasticity, ICTP 2011, 2011, p. 796-801.